Modular DCC micro control unit - Main power module
This main power module, on its own, functions as the minimal DCC micro control unit. Combined with a computer and JMRI software, it is capable of controlling all decoders connected to the rails of the rail network (locomotives, points, signalling, animations, etc.).
The module has various side connectors, enabling it to add new functionalities by connecting different electronic assemblies (Bluetooth joystick, current consumption monitoring, etc.). The BLE joystick module makes the module completely autonomous, eliminating the need for a computer during operation.
Features
The new features in this version are as follows:
- added locomotive presence detection on the programming section;
- addition of a 5V regulator to eliminate dependence on USB power supply (in anticipation of WIFI network control);
- analog current measurement connector added;
- addition of a digital current measurement connector;
- addition of a wireless control connector (BLE or WIFI);
- adjustment of LED protection resistors according to color, to harmonize the visual consistency of the control unit.
Maturité :
Project status
Developments
Electronic schematic (version 1.0)
The heart of this assembly is an Arduino Nano v3 board. Its microcontroller is loaded with the DCC++ program adapted to the characteristics of this circuit.
Commands are sent to the microcontroller either via the serial link (USB) from a computer running the free JMRI software, or via the external DCC control connector (J4).
The DCC signal generated by the ATmega328 microcontroller passes through a power circuit (L298N) before being sent to the rails to control locomotive decoders and various DCC accessories.
Hardware requirements (version 1.0)
Description | Quantity | Reference | Search url |
---|---|---|---|
Tantalum polarized capacitor 1µF | 1 | C1 | |
Capacitor 100nF | 4 | C2, C4, C5, C6 | |
Polarized electrolytic capacitor 470µF | 1 | C3 | |
Polarized electrolytic capacitor 10µF | 1 | C7 | |
Diode 1N4001 | 8 | D1, D2, D3, D4, D5, D6, D7, D8 | |
Pin socket (3x) + pin header (3x) + 3mm two-color LED (green and red), common cathode | 1 | D9 | |
Pin socket (2x) + pin header (2x) + 3mm yellow LED (programming) | 1 | D10 | |
Pin socket (2x) + pin header (2x) + 3mm blue LED (operation) | 1 | D11 | |
3mm red LED (presence detection) | 1 | D12 | |
PCB-mounted 15V power supply jack (5.5 x 2.5mm or 5.5 x 2.1mm depending on transformer plug) | 1 | J1 | |
Rail power supply socket (3-pin, 3.8mm pitch, right-angle for PCB mounting) | 1 | J2 | |
Magnetic connection socket for measuring current consumption (3 pins, 2.8 mm pitch, right-angle for PCB mounting) | 1 | J3 | |
Magnetic connection socket for external controls (4-pin, 2.8mm pitch, right-angle for PCB mounting) | 1 | J4 | |
Magnetic ammeter connection socket (2 pins, 2.8mm pitch, right-angle for PCB mounting) | 1 | J5 | |
Pin header (2x) jumper: short-circuit to avoid using the ammeter | 1 | J6 | |
Transistor NPN PN2222A | 1 | Q1 | |
PNP transistor 2N2907 | 1 | Q2 | |
Resistance 0,1 Ohm (2 W) | 1 | R1 | |
Resistance 1K (1/4 W) | 4 | R2, R6, R7, R12 | |
Resistance 10K (1/4 W) | 3 | R3, R8, R13 | |
Resistance 2K (1/4 W) | 3 | R4, R9, R10 | |
Resistance 4,7K (1/4 W) | 1 | R5 | |
Resistance 220 Ohm (1/4 W) | 1 | R11 | |
Pin header (2x) for emergency stop button (diameter 16 mm) | 1 | SW1 | |
Pin socket (12x) + pin header (12x) of 4RT switch for mode selection (operation / programming). | 2 | SW2 | |
Pin header (2x) for restart button | 1 | SW3 | |
Pin header (2x) for presence detection LED | 1 | SW4 | |
Arduino Nano v3 + pin socket (15x2) | 1 | U1 | |
Double H-bridge L298N | 1 | U2 | |
TO-220 aluminium heat sink 25 x 23 x 16mm with two fixing pins | 1 | Fixation U2 | |
Dual LM358 OP amp + 8-pin DIP support | 1 | U3 | |
5V controller | 1 | U4 | |
Optocoupler 4N35 + 6-pin DIP support | 1 | U5 |
How it works
In progress...
Printed circuit boards (version 1.0)
In progress...
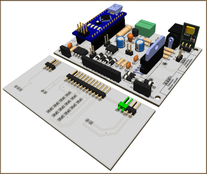
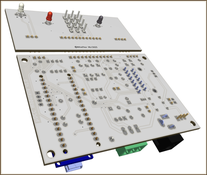
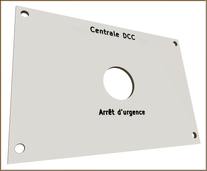
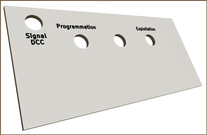
Component installation
Assembly operations
In progress...
Software loaded in the microcontroller
In progress...
Preparing for the first start-up of the micro central unit
In progress...
Power on
In progress...
Network driver software: JMRI
In progress...
A 3D-printed case for a perfect finish...
In progress...
To find out more...
- Locoduino website : the French website dedicated to model railroading. It features many detailed DIY microcontroller-based assemblies. You'll also find tutorials, forums and tests on every subject. It's an inexhaustible source of ideas for building your own layout.
- Download JMRI software : select the JMRI suite download according to your operating system.
- JMRI DecoderPro online help in French.
- GitHub of the original DCC++ open source solution : it's currently the most advanced open source program for building your own NMRA-compliant DCC control unit.
Your e-mail address will not be published. Required fields are marked with *.
Comments
Add comment